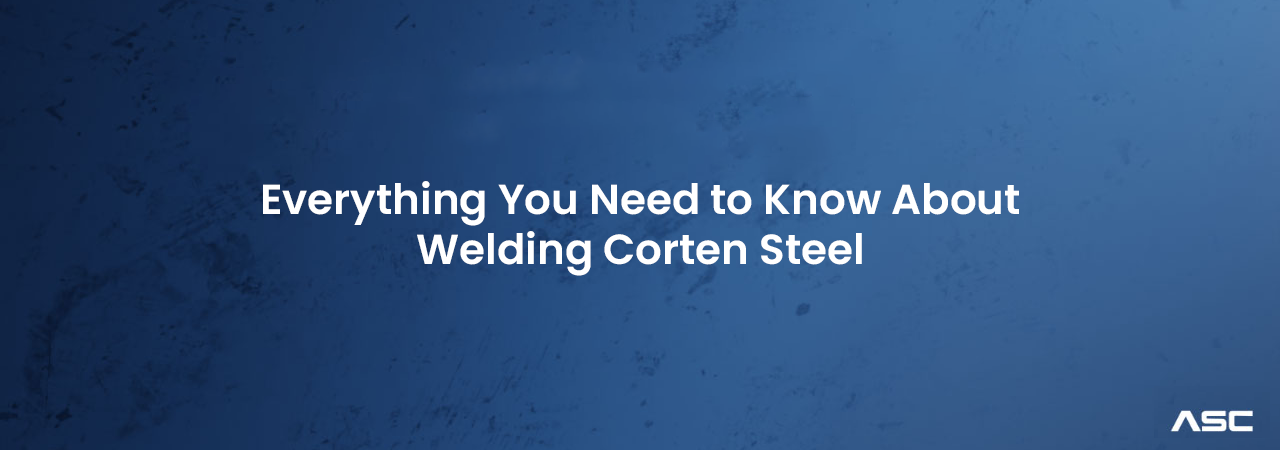
What is Corten Steel Welding?
Corten steel, also known as weathering steel, is a type of steel designed to withstand harsh weather conditions and corrosion when exposed to the elements.
Corten steel properties include high strength, toughness, and ductility, making it a popular choice for outdoor architectural features and sculptures.
The alloy composition of corten steel includes copper, manganese, and nickel, which contribute to its corrosion resistance. A protective layer forms on the surface of the steel, preventing rust and weathering.
Corten steel is particularly well-suited for outdoor applications due to its durability and resistance to corrosion. It remains intact even in harsh environments, displaying high abrasion and fatigue resistance.
Common uses of corten steel include architectural and landscape design, where it is utilized for fences, gates, bridges, and other structures. Additionally, corten steel is often used in the creation of sculptures and decorative items, thanks to its unique aesthetic appeal.
Techniques for Welding Weathering Corten Steel
When it comes to welding weathering corten steel, employing the right technique is crucial for a successful outcome. There are three main techniques commonly used: TIG welding, MIG welding, and Stick welding.
TIG Welding
TIG welding is a precise and clean method, perfect for working with thinner materials. It involves using a tungsten electrode to generate an arc, melting both the base metal and filler material to form a strong and high-quality weld. This technique is particularly suitable for creating detailed welds on weathering corten steel.
MIG Welding
MIG welding is a faster and more efficient option, ideal for thicker materials. It utilizes a wire electrode fed through a spool, which melts and fuses the base metal along with the filler material. MIG welding is excellent for producing solid and smooth welds on weathering corten steel.
Stick Welding
Stick welding is a versatile technique applicable to various materials and thicknesses. It employs a consumable electrode coated in flux, creating a protective shield around the arc to prevent weld contamination. Stick welding is well-suited for creating robust and durable welds on weathering corten steel.
Equipment Required for Welding Weathering Corten Steel
Welding weathering corten steel demands specialized equipment to ensure optimal results. Here’s a list of essential items:
- Welding machine (TIG, MIG, or stick): Choose the appropriate welding machine based on the welding technique preferred for the job.
- Welding helmet: Protect your eyes and face from sparks, UV radiation, and heat with a reliable welding helmet.
- Gloves: Wear heat-resistant gloves to shield your hands from burns and sparks during welding.
- Jacket or apron: Cover yourself with a welding jacket or apron to protect against heat, sparks, and spatter.
- Wire brushes: Use wire brushes to clean the metal surface before welding, ensuring better adhesion and a cleaner weld.
- Clamps: Secure the workpiece in place with clamps to prevent movement during welding.
- Chipping hammer: Remove slag and excess weld material with a chipping hammer to maintain weld quality.
- Respirator mask: Protect your lungs from fumes and airborne particles with a respirator mask, especially when welding in confined spaces or with inadequate ventilation.
Additionally, it’s advisable to use a low-alloy filler metal that matches the weathering characteristics of the corten steel. This ensures a strong and durable weld that complements the properties of the base metal.
Learn the best techniques and materials for welding corten steel with expert help.
Corten Steel Specifications & Grades
Corten steel, commonly known by its trademark name COR-TEN, conforms to specific ASTM specifications outlined below:
- A588: Suitable for structural weathering steel panels, shapes, plates, and bars.
- A242: Intended for steel plates up to 1.5 inches in thickness.
- A606-4: Designed for corten steel sheet and coil applications.
- A847: Applicable for tube and pipe manufacturing.
- A871-65: Pertains to steel plate products with a minimum yield strength of 65ksi.
- A709-50W: Specifically for steel plate usage in bridge construction.
These ASTM specifications ensure that corten steel meets established standards and performance criteria, making it suitable for various construction and industrial applications.
Furthermore, weathering steel grades are available as corten A and corten B. For instance, A242 corresponds to corten A, while A588 corresponds to corten B.
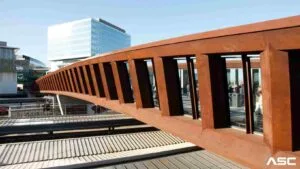
Chemical Composition of Corten Steel
Content, % (ladle analysis) | ||||||||||
---|---|---|---|---|---|---|---|---|---|---|
C (max) | Si | Mn | P | S (max) | Al | V | Cu | Cr | Ni (max) | |
Corten A | 0.12 | 0.25–0.75 | 0.20–0.50 | 0.07–0.15 | 0.030 | 0.015–0.06 | – | 0.25–0.55 | 0.50–1.25 | 0.65 |
Corten B | 0.19 | 0.30–0.65 | 0.80–1.25 | 0.035 max. | 0.030 | 0.020–0.06 | 0.02–0.10 | 0.25–0.40 | 0.40–0.65 | 0.40 |
Mechanical Properties and Thickness Ranges for Corten Steel
Thickness (mm) Strip Products | Plate Products | Yield strength minimum | Tensile stength minimum | Elongation miniumum | |
---|---|---|---|---|---|
Corten A | 2 – 12 | 6 – 12 | 345 | 485 | 20 |
Corten B | 2 – 13 | 6 – 40 | 345 | 485 | 19 |
Corten Grades & Equivalents
Corten | EN 10025-5:2004 |
---|---|
Corten A | S355 J0WP |
Corten B | S355 J0W & S355 J2W |
Heat Treatment of Corten Steel
Heat Treatment | Temperature °C | Treatment Time Manner of cooling |
---|---|---|
Stress relieving | 500–600 (target 580) | 2 minutes / millimetre thickness, minimum 30 minutes Slow cooling in the furnace |
Normalising | 860–940 (target 910) | 1 minute / millimetre thickness, minimum 15 minutes Free cooling in air atmosphere outside the oven |
How to Weld Weathering Corten Steel?
Welding Corten steel can present challenges, but with proper preparation, it can be accomplished effectively.
For thick plates, the initial step involves preheating the metal. This precautionary measure helps prevent warping or cracking during welding. Once the metal reaches the appropriate temperature, welding can commence.
During TIG welding, it’s advisable to utilize a gas lens cup to shield the weld from wind interference, ensuring optimal results. This additional measure helps maintain stability and integrity throughout the welding process.
Welding Preheat & Interpass Temperature for Corten Weathering Steel
When welding Corten steel, preheat and interpass temperatures are important considerations. A preheat temperature of 150-225 degrees Fahrenheit should be used, and an interpass temperature of 400 degrees Fahrenheit should be used. The following are the preheat requirements based on AWS D1.1:
- For plate thickness up to 3/4 inches, no preheat is required.
- For thickness above 3/4 inches, preheat to 100-150 degrees Fahrenheit minimum.
- For thickness above 2.5 inches, preheat to 2
Corten Weathering Steel Welding Electrode/Rods & Welding Wires
- E7018
- E7018-W1
- E8018-W2
- ER70S-2
- ER70S-6
- ER80S-Ni1
- E71-T1C
- E81T1-Ni1C
- E80T-W
Can you weld corten steel to mild steel?
Yes, it’s possible to weld corten steel to mild steel through welding, but it requires careful attention to detail for a strong bond. Welders need to use specific welding methods and filler materials, such as an E7018 electrode, to achieve the desired outcome.
By employing the appropriate welding techniques and materials, skilled welders can establish a durable connection between corten steel and mild steel, ensuring structural integrity and longevity.
Welding Corten Steel To Stainless Steel
Welding Corten Steel to Stainless Steel involves welding two different steel types together. Corten steel develops a rust-like appearance when exposed to the elements, while stainless steel, commonly used in food and medical applications, resists corrosion.
When welding stainless steel to carbon steel, it’s crucial to use a filler metal with the same corrosion resistance as stainless steel. Using a filler metal with lower corrosion resistance could lead to premature corrosion and failure of the Corten steel.
Welding of Corten steel to mild steel, E309L Stick Welding Rod or ER309L TIG-MIG Filler Wire should be used. These filler materials help minimize dilution of the stainless steel when welded with low heat input.
Before welding, it’s essential to clean the weld area thoroughly to remove any contaminants such as paint, grease, or dirt. This can be done using a wire brush or grinder to ensure a clean and strong weld.
What is the best electrode for Corten steel?
Corten Steel Texture
The texture of Corten steel is distinctive, formed through the process of weathering. Its surface can be characterized as rough, rugged, and organic, showcasing a spectrum of earthy hues from rich browns to rusty oranges.
This unique texture imparts a natural beauty and character to Corten steel, making it a favored choice among architects and designers aiming to craft memorable and visually striking pieces.
What Do You Weld A588 Steel With?
In order to weld A588 steel, a welder must use the correct welding rods and electrodes. The alloy steel A588 is composed of carbon, manganese, silicon, phosphorous, and sulfur.
It is recommended that welding rods and electrodes used to weld this type of steel have a high manganese content.
Can You Weld Corten Steel With 7018?
Corten Steel Strength And Weakness
Corten steel, renowned for its durability and strength, is widely recognized for its resilience in outdoor applications. However, it does possess certain weaknesses that should be acknowledged.
One of Corten steel’s weaknesses is its susceptibility to rust if not adequately maintained, leading to potential corrosion and damage over time. Additionally, Corten steel may experience deformation over time, particularly if subjected to insufficient support, causing stretching and sagging.
Despite these weaknesses, Corten steel remains a viable choice for various projects. With proper maintenance and installation, its beauty and functionality can endure for many years.
Corten steel, also known as weather-resistant steel, is primarily composed of materials such as copper, chromium, and nickel, imparting weather-resistant properties. Unlike painted steels, Corten steel forms a stable rust-like appearance when exposed to prolonged weathering.
This natural rust-like surface acts as a protective barrier against corrosion, self-repairing over time and preventing further deterioration. Due to its unique appearance and weather-resistant characteristics, Corten steel is commonly utilized in outdoor sculptures and architectural features, showcasing its enduring appeal and versatility.
Corten Steel Uses and Applications
Corten steel is a sought-after material in architecture and design, prized for its distinctive rusted appearance and robustness. Here are some prevalent uses and applications of corten steel:
- Building Facades:Â Corten steel is frequently employed in building facades and exterior cladding, adding an industrial chic aesthetic with its rusted appearance.
- Sculptures:Â Its unique look makes corten steel a favored material for sculptures and public art installations, lending them an intriguing visual appeal.
- Garden Design:Â Corten steel finds popularity in garden design, utilized for planters, retaining walls, and edging due to its rustic appearance and resilience.
- Roofing and Fencing:Â Corten steel is chosen for roofing and fencing applications, benefiting from its weather-resistant properties and striking visual impact.
- Bridges and Infrastructure: Corten steel’s strength and durability make it a preferred choice for bridges and various infrastructure projects, ensuring long-lasting performance even in challenging environments.
- Interior Design:Â Corten steel is increasingly used in interior design, adding character to spaces through furniture, accent walls, and other decorative elements.
FAQ’s
Standard welding equipment can be used, but proper techniques and filler materials specific to Corten steel are essential for the best results.
When arc welding Corten steel, use a low-hydrogen electrode or a filler material designed for weathering steel to maintain its corrosion-resistant properties. Proper preheating and post-weld cleaning are also recommended to ensure strong, durable welds.
For MIG welding Corten steel, use a filler wire that matches the alloy composition of the steel, such as ER70S-6. Ensure proper shielding gas, like 75% argon and 25% CO2, to prevent oxidation and maintain the steel’s corrosion resistance.
A588 welding wire is specifically designed for welding weathering steels like Corten steel (A588). It ensures a strong, durable weld with good corrosion resistance, maintaining the steel’s protective rust layer.
The best method for Corten Steel welding is using a compatible filler material like ER70S-6 for MIG or TIG welding. Proper preheating and post-weld cleaning are essential to preserve its corrosion-resistant properties.
To weld Corten steel, use a weathering steel-compatible filler material like ER70S-6. Preheat thicker sections to avoid cracking, and clean the weld area to ensure a strong, corrosion-resistant bond.
Corten rods are commonly used in outdoor construction and artistic applications, such as sculptures, railings, and architectural elements. They are made from weathering steel, which develops a protective rust layer, providing both aesthetic appeal and enhanced durability against corrosion.
Yes, Corten steel can be welded using appropriate filler materials like ER70S-6. It’s important to follow proper welding techniques, such as preheating thicker sections and ensuring post-weld cleaning, to maintain the steel’s corrosion resistance.
Corten welding wire is specifically designed for welding weathering steels like Corten steel. It ensures strong, durable welds that maintain the steel’s corrosion-resistant properties, helping to preserve its unique rusted appearance.
Contact Our Expert Team Now
Corten Steel Tube is a leading supplier of high-quality Corten steel products in India. We offer a wide range of Corten steel sheets, plates, and custom sizes, supported by cutting-edge fabrication and processing services to meet your project needs.
Leave A Comment