Understanding the Different Types of Carbon Steel Flanges
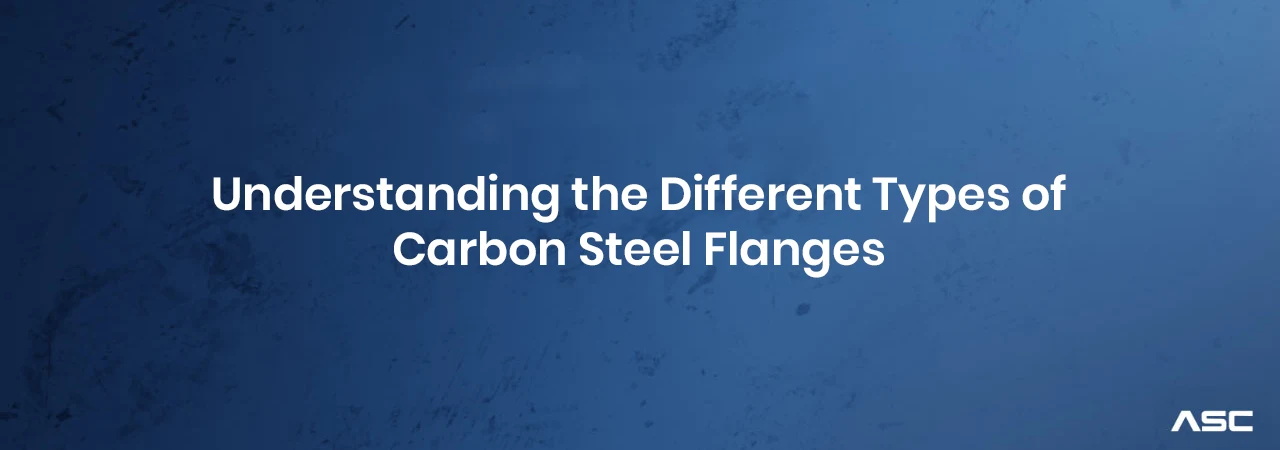
Flanges constructed from carbon steel are essential components for connecting valves, hoses, and other machinery in a number of industries. Carbon steel flanges are commonly utilized in petrochemicals, production, oil and gas, and electricity generation sectors because of their resilience, resilience, and pricing. We will look over a variety of carbon steel flanges, their specific applications and the factors to take into consideration while choosing the most suitable flange for your needs in this detailed blog.
What are Carbon Steel Flanges?
Connectors made from carbon steel, an alloy primarily composed of carbon and iron, are known as carbon steel flanges. In the plumbing sector, these flanges are developed to provide secure, waterproof connections among pipes or machinery. They have become a common choice in several industrial uses due to their affordable price and durability in extreme pressures and temperatures.
Different kinds of carbon steel pipe flanges can be purchased depending on the alloying elements, mechanical properties, and level of carbon. The most commonly used grades are ASTM A105, ASTM A350 LF2, and ASTM A694, each one of which consists of unique properties for different kinds of applications.
Common Types of Carbon Steel Flanges
- Weld Neck Carbon Steel Flanges – A long, curved hub that gradually merges into the pipe or fitting’s thickness is what differentiates weld neck flanges. By reducing stress levels this design maintains structural integrity and lowers the risk of leakage in high-pressure areas and extreme temperatures. For crucial uses where reliability and security is essential, like in the petroleum, oil & gas, chemical manufacturing, and electrical power industries, weld neck flanges are ideal. They are often used in averse areas that are essential piping systems due to their strong design.
- Slip-On Carbon Steel Flanges – Slip-on flanges are welded together to create a strong connection, and then they have been designed to move easily across the pipeline. They are affordable, easy to set up, and suitable for applications demanding moderate to medium pressure. If rapid installation is required but accuracy isn’t equally essential, slip-on flanges are the more suitable option. They have become prevalent in numerous sectors due to their reliable functionality in smaller-scale settings, but they’re not as durable as weld neck flanges.
- Blind Carbon Steel Flanges – Blind flanges are robust disks without a central bore which can be utilized to separate sections of the piping network or simply to seal pipe ends. They are essential to activities requiring repair, maintenance, and hydraulic monitoring. Blind flanges are beneficial in industries such as petrochemical products, oil refineries, and electrical power generation due to their versatility and capacity to cope with a variety of atmospheric pressure levels. This makes them an ideal choice for reliable sealing as they endure extreme pressure without leakages.
- Threaded Carbon Steel Flanges – Internal threads on threaded flanges allow them to be easily screwed on a pipe’s external threads. These types of flanges are ideal for non-essential, low-temperature circumstances while welding is not necessary or possible. Plumbing and fire fighting equipment belong to two businesses that often employ threaded flanges. They are perfect for short-term installations or equipment that require regular service due to their simplicity the process is to set up and remove them.
- Socket Weld Carbon Steel Flanges – Adequate protection against leaks is offered by socket weld flanges, that consist of an opening in which the pipe is screwed and welded. They are prevalent in hydraulic structures, chemical production, and steaming distribution pipelines, and they tend to be used in small-diameter, extremely high-pressure piping systems. The precise connection is feasible because the internal socket design reduces the potential of alignment and enhances the system’s efficiency as a whole.
- Lap Joint Carbon Steel Flanges – The stub end fittings are used with lap joint flanges to allow smooth movement and positioning throughout construction. They are ideal for systems which require to be dismantled regularly for servicing, cleaning, or examination. Despite the fact that they are not as durable as slip-on or welded neck flanges, they can be helpful in industries like food manufacturing, water purification, and pharmaceutical companies due to their versatility and longevity.
Choosing the Right Carbon Steel Flange
- Application Requirements – The first step is to examine the specific demands of an application. This involves being informed of the humidity, operational stress and type of fluid that is being carried. For example, a weld neck flange may be more suitable if the system has been exposed to extremely high temperature or pressures. But a slip-on flange may be suitable for noncritical, low-pressure uses. To ensure consistency and durability, one must additionally analyze the fluid’s qualities, particularly if it is toxic, ignited aggressive, or non-corrosive.
- Grade Selection – There are multiple types of carbon steel flanges, each designed to resist specific conditions. For mild temperature and pressure situations, ordinary grades like ASTM A105 and ASTM A350 LF2 are commonly used. But if the appliance is exposed to adverse environments like chemicals or humidity, you may choose to opt for a higher-grade steel with carbon content flange which has greater resistance to corrosion. Making an informed choice can be supported by communicating with manufacturers or suppliers regarding the ideal grade in your project.
- Flange Type – It’s essential to understand how various flange type operate effectively. Slip-on flanges are appropriate for applications with lower pressure, while weld neck flanges are most suitable for high-pressure areas and crucial uses. Threaded flanges are advised for circumstances when welding isn’t possible, whereas blind flanges are used for closing. Elbow joint flanges are ideal for equipment that require to be dismantled regularly while socket weld flanges enable a tight fit for small tubes under high pressure. Choosing an appropriate flange type will be assisted by evaluating your structure’s installation and maintenance needs.
- Size Compatibility – It is important to ensure that the selected flange meets the pipe’s measurements and schedule. Water loss, higher maintenance expenditures, and service issues could result from mismatched sizes. When finalizing the purchase, verify the timeline, pressure evaluations; and nominal pipe size (NPS). Also, take into consideration any specific laws or industry standards that could be associated with your plumbing system.
Conclusion
For combining pipes and equipment in a variety of industries, carbon steel flanges provide a reasonable and versatile solution. You can guarantee safety, reliability, and effectiveness in your piping systems by making accurate choices and becoming informed about the numerous types of carbon steel flanges and their applications.
For high-quality carbon steel flanges from reliable suppliers, visit Corten Steel Tube.