APH Tubes: A Complete Guide to Material and Specifications
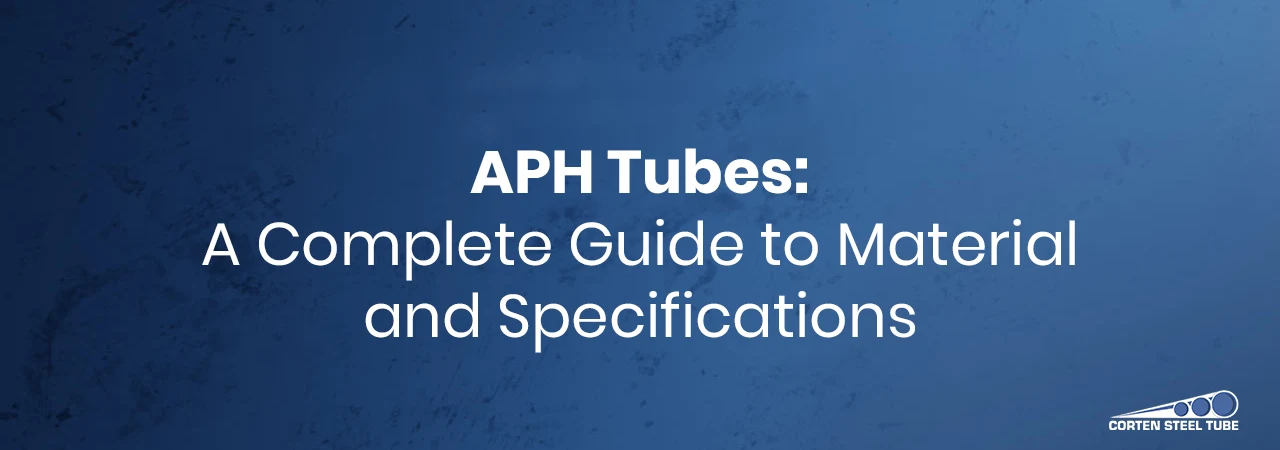
APH tubes find extensive application in several industries, notably in power generation, in coal, gas and biomass power plants. APH tubes boost boiler efficiency like cement production, the tubes serve in kilns to intensify the combustion process and reduce energy consumption. Steel manufacturing APH tubes aid in aiding the heating of air for furnaces, thereby improving energy efficiency in furnaces.
What Are APH Tubes?
Air Preheaters (APH) are shell and tube type heat exchangers that are used to preheat the air before it goes into the boiler or furnaces to burn fuels. The main job of an air preheater is to take heat from the flue gases coming out of the boiler.
How Do APH Tubes Work?
APH Tubes, or tubes of air preheating, are essential components in enhancing energy efficiency in industrial systems, specifically in boilers and furnaces. Here is a streamlined description of their operation:
- Over the Air Preheater Tubes Pass Hot Flue Gases – In systems that combust fuel, like combustion engines, hot combustion gases called flue gases are normally vented to the atmosphere. Instead of letting this heat go to waste, the flue gases are diverted to flow over or around the tubes of the Air Preheater.
- Tubes Absorb Heat from the Gases – Made from metals that resist high temperatures, the tubes of the APH absorb heat from the hot flue gases that pass by them. This process is similar to how a metal spoon becomes warm when it is stirred in hot soup. The tubes in the APH effectively soak up the heat.
- Cold Air Flows Through or Around the Tubes and Gets Heated – Simultaneously, the uncombusted air that is routed to the combustion zone is made to flow in a manner through or around the now heated tubes of the space heating installation. The tubing, which is part of an extensive series of long, narrow, flue-like channels, obstructs the passage of the air even more than it does when the tubing is ambient-temperature cool. Consequently, the long passages, with air pushed through or around them by the strong draft in the combustion zone, ensure that most of the air gets heated before flowing to the combustion chamber.
Specifications of Air Preheater Tubes (APH)
When detailing the specifications of Air Preheater (APH) tubes, it’s vital to consider the demanding operational environment they endure. Here’s a breakdown of key specifications:
Thickness | 0-10mm |
---|---|
Length | 5-15 m |
Material | CORTEN STEEL |
Features | High Quality |
Finishing | Polished |
Applications of APH Tubes in Different Industries
Everywhere a heat-intensive industry needs heat, APH tubes pay off. By taking heat from exhaust gases and using it to preheat air before combustion, they help save fuel, cut costs, and protect the environment. Here are a few APH tube utilizers:
- Power plants: APH tubes help preheat the air used to ignite the fuel in large combustion turbines.
- Cement plants: APH tubes work with similar processes, substituting the air-fuel mixture that power plants use with the sort of mix that cement kilns need.
- Steel mills: In electric arc furnaces, which are basically huge, superheated APH tubes turned on their sides, the steel goes in, the flames come out, and the useful heat winds up in the APH tubes
How APH tubes help:
Heat is captured by the APH tubes from the flue gases. They warm the air that enters the boiler. That air is at a temperature much closer to what’s needed for combustion than is typical in today’s coal-fired power plants. Thus, less fuel is needed to achieve the desired temperature.
- Power Generation Plants : In power generation plants, it is big boilers that generate the necessary steam to drive the turbines for electricity production.
- Petrochemical Industry : This industry involves the refining of crude oil and the production of fuels, chemicals, and plastics several of which must be heated to serve their end-demand.
- Cement Plants : Cement production consists of heating raw materials in large kilns.They preheat the air entering the rotary kiln, enabling faster temperature achievement and maintenance, resulting in higher productivity, less energy cost, and fewer emissions.
- Pulp and Paper Industry : Paper mills need substantial heat for the drying of pulp and paper sheets. They make sure that the air used in the drying sections is preheated, which reduces fuel needs, speeds up drying times, improves energy efficiency, and provides steady product quality.
- Steel and Metallurgy Plants : The making of steel and metals requires high-temperature intensive heating in furnaces, using huge amounts of energy.They preheat the air for furnaces by recovering heat from flue gases, using the heat to warm the air that goes into the furnace and makes the furnace more efficient, using less fuel and lasting longer.
Benefits of Using APH Tubes
Integrating APH tubes in industrial plants is beneficial for several reasons:
- Improved Energy Efficiency: Recovered heat is used to preheat air; consequently, less fuel is consumed to provide the same amount of energy in the combustion system.
- Reduced Carbon Intensity: The air preheating system uses roughly one-third of the energy produced by combustion. Therefore, the air preheating system can be seen as a means to reduce carbon emissions on a large scale.
- Cost Reduction: The system reduces operational costs as the industrial process becomes more energy-efficient.
- Enhanced Equipment Performance and Lifetime: The reduction of thermal stress on the air heater improves the performance of industrial equipment and extends its working life.
Key Materials Used in APH Tubes Manufacturing
Selecting the appropriate material for an APH tube is key to ensuring adequate performance and durability.
- Carbon Steel: An inexpensive and widely used option for APH tubes, it performs well in most moderate temperature environments.
- Alloy Steel: Delivers better heat and strength performance, making it a suitable option for a number of reasonably intense applications.
- Stainless Steel: The ideal choice for any thermodynamic converter application that exists in a corrosive environment.
- Corten Steel (Weathering Steel): Incredibly durable, with outstanding resistance to weather and atmospheric conditions and a suitable option for APH tubes in such environments. The selection of any one material over another depends largely on the temperature, environment, and the composition of the flue gas to which the tube will be exposed.
Factors to Consider When Choosing APH Tubes
When picking the proper APH tube for your system, take into account these factors:
- Heat Resistance and Durability: Make sure the material can take high temperatures and steady thermal cycling without falling apart.
- Cost-Effectiveness and Efficiency: Weigh initial outlay against long-term performance to get the best return on investment.
- Compatibility with Industrial Equipment: Tubes should work with your existing boiler or furnace, and that means they need to be the right size, handle the right pressure, and connect in the right way.
Maintenance and Cleaning of APH Tubes
Proper upkeep is key to ensuring APH tubes work well and
- Regular inspections: See that there are no signs of corrosion, scaling and blockage.
- Mechanical cleaning: Use soot blowers and brushes to keep the deposits from building up too much.
- Clean them chemically when necessary: That would be when their deposits don’t appear to be coming off well with mechanical means.
- Check for leaks: You know how to do that. Report leaks when you find them, and be sure to replace any tubes that are unduly leaky.
Common Issues and Troubleshooting in APH Tubes
Some common problems seen with APH tubes are these
- Corrosion: Caused by flue gases or condensation that are too acidic.
- Fouling and Scaling: Due to too much ash, soot, or unburned residues.
- Cracking or Tube Failure: From thermal stress or poor material choice.
To fix these problems:
- Use materials that resist corrosion.
- Keep the combustion assemblies burning completely, too rich or too lean makes for a hot and/or too wet exhaust, and this will corrode!
- Measure and monitor.
Future Trends and Innovations in APH Tube Technology
Tube technology keeps getting better for industries aiming for higher efficiency and lower emissions. The latest innovations include the following:
- Coatings: Anti-corrosion and anti-fouling coatings are extending tube life.
- Monitoring: Real-time sensors keep tabs on temperature and other vital signs.
- Alloys: New materials with better heat and anti-corrosion resistance are in the mix.
- Designs: Even as they save space, new configurations are enhancing tube performance.
- And with that, on to some touches of elegance in tube technology.
Conclusion
The primary component in contemporary heat recovery systems are air preheater tubes. These tubes offer enhanced energy efficiency, reduced emissions and lower costs in a variety of settings, including petrochemical factories and power plants. Making better decisions on the operations of your plant will be possible if you have a thorough understanding of its applications, materials, maintenance requirements and future trends.
For ideal performance,choose high-quality air preheater tubes by Corten Steel Tube designed for your specific operational requirements and maintain them regularly.